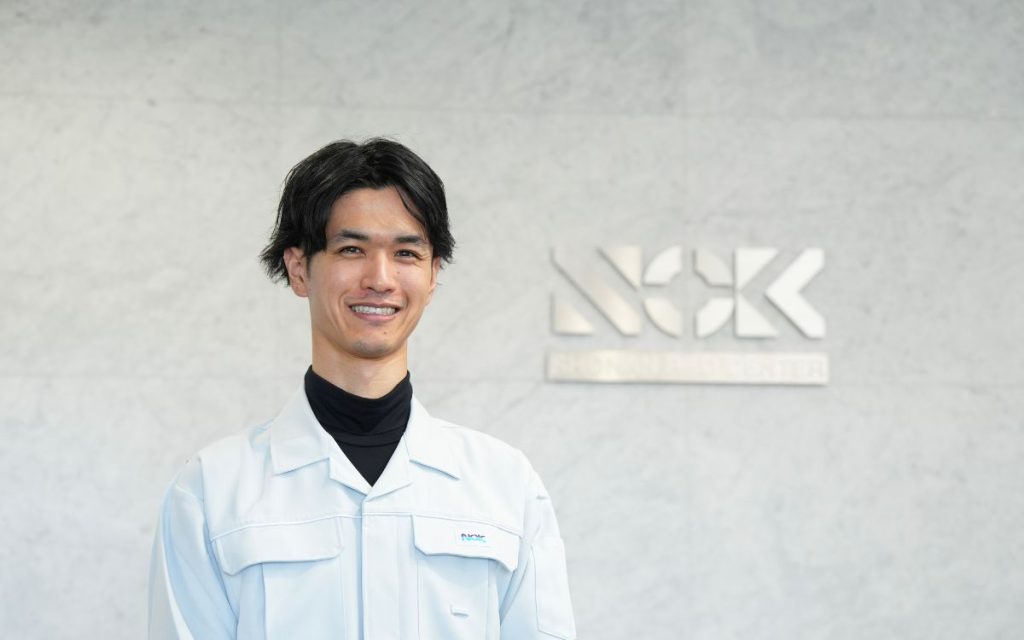
生産技術職として大きな飛躍にチャレンジ。NOKで実感する、ものづくりの醍醐味。
生産技術職として大きな飛躍にチャレンジ。
NOKで実感する、ものづくりの醍醐味。
このストーリーのポイント
- 人々に不可欠な部品を通じて社会貢献したい
- 困難なラインの立ち上げに挑戦し、成長を実感
- 海外での技術発表などによって自分の可能性を高めていく
ものづくりを通じた社会貢献に惹かれ、NOKに入社。生産設備の設計を通じて、ものづくりの現場を支えていることにやりがいを感じている。若手のうちから伸び伸びとチャレンジさせてくれるカルチャーが嬉しい。
NOK株式会社
松尾 雄太
NOKグループ R&D製法開発部
Operation Engineering課主事補
2014年入社
福岡県出身。学生時代は機械系を専攻し、材料強度についての研究に取り組んだ。高い技術力と人間関係の心地よさに惹かれてNOKに入社。以来、生産技術部門に所属し、設備の設計・開発に従事する。趣味はゴルフ。月に一回はコースに出ている。
変革期に真価を発揮する、優れた技術力
子供の頃から機械いじりが好きで、高校では物理が得意だったことから、自然と機械系の学びを志すようになりました。
大学で印象に残っているのは、設計の授業です。歯車減速機、いわゆるミッションの設計を学んだのですが、その中でオイルシールを選定する際に手にしたカタログについていたのがNOKのロゴ。それまでオイルシールという部品のことは知らなかったので、油の漏れを防ぐためにこんな部品があるんだと驚いたものでした。これがNOKとの出会いでした。
就職活動に際して私の考えた“軸”が、技術者として広く社会の役に立ちたいということでした。そのとき頭に浮かんだのがNOKのロゴです。自動車や産業機械、さらにはデジタル機器に不可欠のフレキシブルプリント基板などにNOKグループの部品が広く使われていることを知り、まさに様々な領域で社会に貢献している会社であることに惹かれました。道路の中央線や分離帯などに設置されている交通安全用品も製造しているとのことで、親しみも感じました。
社風にも惹かれました。セミナー等では採用担当者同士がフランクに話し合っていて、とてもアットホームな雰囲気を感じました。この印象は入社しても変わらず、部署や年次の垣根を感じることなく気軽にコミュニケーションできる環境です。
また、高い技術力も入社の決め手となりました。自動車産業は100年に一度と言われる変革期を迎え、ガソリン車からEVへのシフトが進んでいます。このような変化の中にあってもNOKならば高い技術力を活かし、EVに不可欠の部品を開発することができるでしょう。世の中のトレンドが変わってもきっと社会貢献を続けることができる、そんな優れた技術力があると感じて入社を決めました。
生産拠点への異動で、技術者としての幅を広げる
入社以来生産技術部門に所属し、生産設備の設計・開発に従事してきました。
最初は右も左も分からない中、先輩の指導のもとで生産設備の設計を担当。どうにか設計したものの、テストをしたら動かなくて、その原因を分析してまた設計をやり直すことの繰り返しでした。
失敗しても叱られることはなく、それも貴重な経験として次に活かせばいいと言われたものです。チャレンジさせることで若手を育てていく、そんなNOKのカルチャーを感じました。
大きな成長を実感したのは入社4年目、ジョブローテーションで静岡事業場に異動したときのことです。
それまでの私は研究拠点である湘南R&Dセンターで生産設備の設計に携わっていました。基礎を一通り学んだ段階で、実際に生産設備がどのように使われているのか、身をもって体験するために異動することになったのです。これは私にとってとてもいい経験になりました。
生産現場では、何らかのトラブルで設備が止まってしまうと、製品づくりそのものが即ストップしてしまいます。新しい装置を導入したのに動かないという連絡を受けて、大急ぎで現場に駆けつけたこともあり、いかに現場での使い勝手や機能を考えて設計することが大切かということを学びました。そのために現場で装置を操作する方々の意見にも耳を傾けました。
ものづくりに貢献している実感と同時に、その責任の重さを改めて実感したものでした。
静岡事業場で2年間を過ごした後、湘南R&Dセンターに戻ってきて担当することになったのが、自動車向け新商品の製造ラインの導入プロジェクトでした。新規ラインの立ち上げに際し、その一つの工程を私が任されることになったのです。
生産プロセスの省人化を目指して自働化設備を導入するというのがその製造ラインのコンセプトでした。一番の難点はそれまでにないまったく新しい形状の部品をロボットで運ばなくてはならないという点で、設計者にとって非常に高いハードルだと感じましたが、一方で静岡事業場での2年間で培った経験や知見を活かせば絶対に自分にもできるはずだという自信はありました。
入社7年目のチャレンジです。そろそろ中堅というキャリアに差しかかった私に思い切ったチャレンジをさせてくれることでさらなる成長を促そうとする会社の期待が感じられ、大いに燃えました。
設計を担当した生産設備は、手塩にかけた“我が子”
NOK生産技術では、自分たちで設計図を書く機会もあり、普段はNOK設計とメーカー設計とを状況に応じて使い分けています。技術者は仕様書を取りまとめるだけで、設計は外部の協力会社に発注するという会社もある中、現場の要望をヒアリングしながら、要望に応える機能を具現化するために自ら設計できることは、ものづくりの喜びです。時には「こんな機能が欲しいが装置はコンパクトに」という相反する要望に頭を悩ませることもあるものの、先輩や上司と話し合いながら解決策を探っていく課程は、とても面白いです。
今回の設備ではロボット搬送が課題であったため、治具・テスト機を制作して搬送の実験(検証)を実施した上で、結果が良好であった機構を装置メーカーに提示し、設備に落とし込んでいただきました。そして、組み立て、完成検査という工程を経て、この新しい製造装置は生産現場に据え付けられました。
それまで私が発注者であるNOKの代表として装置メーカーとやり取りを進めたのですが、図面を渡して終わりではないところもこの仕事の面白みで、社内の品質管理部門なども含め、私が周囲を巻き込みながらプロジェクトを進めていく実感がありました。
生産技術職といっても向き合うのは装置ではなくて人間です。装置メーカーを含め、大勢の方とコミュニケーションを重ねる必要がありますから、コミュニケーション力は非常に重要だと感じました。こちらの意図が正しく伝わっていないことも多々あり、打ち合わせを重ねながら細かいところを詰めていきました。
作った設備が据え付けられた後も、私の仕事は続きました。実際に量産が始まってから、形状にバラツキが生じていたのです。連絡を受けた私はそのつど湘南R&Dセンターから出向いていき、実際に装置が稼働している様子やバラツキの状態などを自分の目で確認して、細かな調整を続けていきました。
連絡を受けた段階で状況と原因、対策について、ある程度の目星をつけながら現場へ飛んでいくわけですが、その際は静岡事業場に異動した2年間の経験が活きていると実感しました。
据え付けてから半年ほどはこうした改善を続け、現在、この生産設備は順調に稼働を続けています。まるで自分の子供を世の中に送り出したような気持ちであり、問題なく動いているという報告を耳にすると、我が子の活躍ぶりにホッとしつつも誇らしくなる、そんな気持ちを感じます。
海外でのプレゼンテーションも経験し、ステップアップへ
現在私が担当しているテーマが、東北地区の生産設備の自働化です。製品検査の工程で、これまで作業者が手作業で行っていたものをロボットが行うように置き換えていくという取り組みです。自働化の取り組みは今後各生産拠点でも展開されていくことになると思うので、私にとって非常にやりがいのあるものです。いずれAIの導入も視野に入ってくるでしょうし、こうした先端のテクノロジーに触れられることも技術者としてのやりがいです。
私は機械の専門家ですが、実は静岡事業場時代、電気工事士の資格を取得しました。当時の上司の「装置は機械だけでなく、電気とプログラムの力で動いているのだから、全部理解できるようにならないと」とのアドバイスを受けてのことでした。実際、資格を取得してからは装置への理解も深まったと感じています。上司のアドバイスには感謝しています。
電気工事士の資格取得に際しては、試験費用はもちろんのこと、実務試験の必要な工具の購入費、講習会の参加費、参考書等の購入費など、一切の費用を会社が負担してくれました。非常に恵まれていると感謝しています。
こうしたサポートを活かし、今は英語の学習に取り組んでいます。
実は一昨年、ドイツで開催された技術交流会に参加させていただき、パネルディスカッションで発表する機会をいただきました。大勢の外国人技術者の前での英語でのプレゼンテーションは人生で最も緊張した体験でしたが、大きな拍手をいただいたこともあって自信につながりました。この経験をこれからの成長につなげていくためにも、英語の学習には力を入れていきます。
今後の目標は、生産設備の自働化という大きなミッションをやり遂げることと、海外拠点に出向することです。それによってNOK全体を俯瞰する力を身につけ、生産設備のことなら何でも任せてもらえる存在になりたいと思っています。
私のチャレンジはこれからも続いていきます。