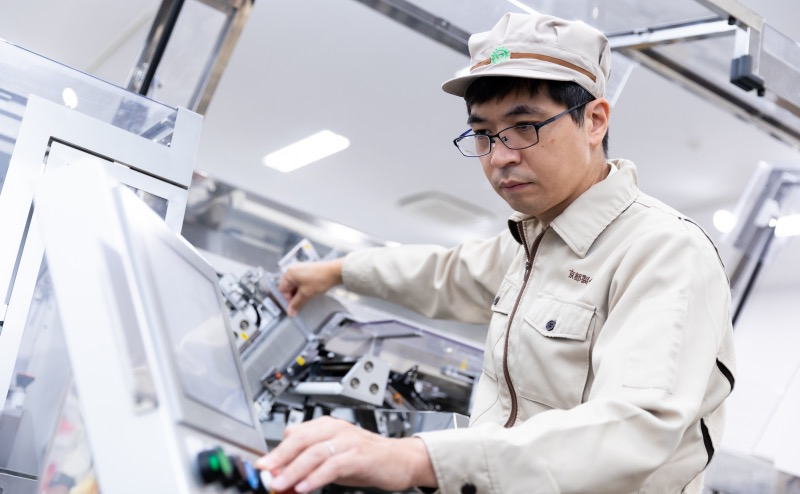
会社初!“人をダメにする機械”。技術者にとって最高の褒め言葉だと思いました。
このストーリーのポイント
- オーダーメイドの産業機械を完全自社開発する京都製作所に就職
- 後に会社の「標準機能」となるような開発を次々に手がける
- クライアントからは「人をダメにする機械」という最高の評価も
入社以来14年、一貫して機械の頭脳ともいうべきシステム設計・制御設計に従事。会社として初めての開発、後に京都製作所の機械の標準機能となるような開発など、重要な仕事を数多く任されてきた。機械としての性能だけでなく、常にユーザーの使い勝手を重視する姿勢が、会社からもクライアントからも高く評価されている。
-profile-
谷川 聡
株式会社 京都製作所
技術部 応用開発グループ長
2007年4月入社/富山大学 電気電子工学科卒
実家が木工所を営んでいたこともあり、幼い頃から「モノづくり」が好きだった。中学の技術の授業での電気工作がきっかけで、機械に興味を持つ。大学は電気電子工学科に進み、いよいよ機械設計の道へ。完全オーダーメイドの機械づくりを行う京都製作所と出会い、2007年4月に入社し、現在は応用開発グループ長として活躍している。
新しい機械を、最初から最後まで自分でつくりたい
大学に入った頃はまだ漠然と「モノづくりに携わる仕事がしたい」と思っている程度でした。ただ就活が近づくにつれ思いが具体化し、「できれば新しい装置を最初から最後まで自分の手でつくってみたい」と考えるようになっていました。そして出会ったのが京都製作所という会社です。まず、この世に一つしかないオーダーメイドの機械をつくっている。基本的に構想、設計、立ち上げ、調整、現場への設置まで、一人の設計担当が責任を持って行う。こんな仕事環境は私が就活で知り得た会社の中に、一つもありませんでした。さらに会社見学の際に実際に動いている機械を見て、自分もこういう機械の設計にぜひ携わりたいと強く思いました。
京都製作所は様々な産業機械をつくっていますが、標準機としていくつかのカートナーやケーサーもラインナップされています。「カートナー」とは食品・医薬品などを化粧箱梱包する機械。例えば生産ラインを流れてくる食品を、向きを揃えながら一定数ずつをまとめ箱に詰めるような仕組みで、日本の多くの大手メーカーに導入されています。「ケーサー」は段ボールの製函・充填・封緘までを全自動で行なったり、Blue-rayなどのディスクを1枚1枚プラスチックケースに収めてパッケージングしたりする機械。こちらも圧倒的なスピードと正確性に定評があり、国内外の企業で使われています。
こうした機械を、対象となる商品の大きさや形状、工場の環境やスペースなどに合わせて一台一台、設計・開発していきます。まさに一品一様のオーダーメイド。その中で私は開発部に所属し、主にシステム設計や制御設計を担当してきました。もちろん仕事ですから予算や開発期間も限られています。時にはやりたいことと現実の間で悩んだり、よりよい品質・サービスを提供するために頭を抱えたりすることもありました。しかしお客様に寄り添い、他部署の協力を得ながら完成させたときの達成感は格別。14年の中で「これは京都製作所でしか経験できない」と思えるような仕事がいくつもありました。
後の京都製作所の「標準機能」となる開発
これは入社5〜6年目の仕事。京都製作所の主力機械である「VARIOシリーズ」の開発に携わりました。VARIOは主に医薬品・化粧品・食品業界で活躍するカートナーで、この新型機の開発と同時に、シリーズ全体の使い勝手・操作性・機能を向上させるというミッションです。機械設計担当、製造担当と力を合わせ、営業やお客様からも情報収集しながら、開発チームとして最高の環境で仕事ができたことを、よく覚えています。
まずは実際にVARIOシリーズを導入いただいているお客様から、操作性・問題点・改善点をヒアリング。機械の調整を担当する製造部からも要望を聞き出しました。結果、機械の兼用の際に「多品種であればあるほど部品も多くなり、交換に時間がかかる」「部品が多いため似たような兼用部品を間違え、品質が担保されない」「最悪、部品間違いによって機械の破損が発生し、生産が止まってしまう」というような話を吸い上げることができました。「兼用」とは、同じ機械で大きさや形状の違う商品を箱詰め・梱包すること。簡単にいうと300mlのペットボトルと500mlのペットボトルの箱詰めを1台の機械にやらせるという感じですね。昨日まで300mlの箱詰めをしていた機械を、今日から500ml用に切り替える。その際に設定を変更したり、一部の部品を取り替えたりという作業が必要になるのです。
私たちが目指したのは「完全兼用レス化」。つまり兼用にかかる手間や時間を、一切なくしてしまうことです。手動兼用箇所をサーボ化(自動制御化)し、紙媒体で兼用していた箇所をデータで管理できるよう改良。どうしても手動で部品脱着を行わざるをえない部分も、RFIDにより兼用部品の照合を行う仕組みを開発し、兼用ミスを極力低減するようにしました。RFIDとは、電波を用いてRFタグのデータを非接触で読み書きするシステムです。バーコードでの運用だとタグを1枚1枚レーザなどでスキャンしますが、RFIDの運用では複数のタグを電波で一気にスキャンできます。だから電波が届く範囲であれば、遠くのタグも読み取りが可能なのです。これを新型VARIOで評価・検証した結果、既存機からの大幅な改善を実現。機械操作を行うオペレーターの習熟度に関わらず、誰でも機械の型替えができるようになりました。いまでは当たり前となっているサーボモータによる自動兼用の先駆けといえます。この開発を経て、京都製作所の機械の標準となった機能も数多くあり、思い出深い仕事の一つとなっています。
人をダメにする機械というお客様からのお言葉
医薬向けの段ボールケーサーの開発では、日本を代表する大手ロボットメーカーの多軸ロボットを取り入れたことがありました。従来のケーサーでは様々な形状・大きさの製品に対応するため、集積装置を都度変更し、製品を移動させる移載装置のヘッドも取り替える必要がありました。しかしケーサーという機械の性質上、移載装置のヘッドが大型化し、人の手で交換することが難しく、このユニットの代替として大手ロボットメーカーの「6軸多関節ロボット」を採用することになったのです。
しかし京都製作所ではこのロボット用のソフトを自社設計したことがなく、完全にゼロからのスタートとなりました。まず前提として様々な製品に対応できること。そして現場で機械を動かす人の操作性を考慮することが求められました。一般的な多関節ロボットのプログラムは教示ベースの考え方で組まれ、現場で少しずつ教示ポイントを修正すればロボット軌跡の細かな調整が可能です。ただポイントを増やせばその分、品種が多くなるにつれて調整箇所も増えてきます。これでは都度ポイントを変更・調整するなど、作業者に相応の操作技術が必要で、結局「使い勝手の悪い機械」「扱いにくい装置」になってしまいます。そこでまず教示ポイントを極力減らし、ある程度であれば経路や作業位置の変更をタッチパネルから数値データで変更できるように設計しました。
また当時の多軸ロボットは搬送する製品の重量や慣性を設定することで軌跡制御、過負荷検知を行える機能を有していたものの、その設定可能数は有限で、さらに設定を切り替えるためには教示操作盤を操作する必要があったのです。そこで大手ロボットメーカーの研究所に、外部からのデータで負荷設定をより動的に切り替えられる機能の追加を依頼。当時は京都製作所だけに提供される特別オプションプログラムでしたが、いまではそのロボットメーカーの多軸ロボットに標準搭載されています。
こうして完成させた機械の市場投入第1号、大手製薬会社様向けの装置担当も私が担当しましたが、納入から1年後に現場を訪問した際、トラブルもほとんどなく順調に稼働している様子を見たときは一安心しました。さらに担当者からこんな言葉もいただいたのです。「うちの社内でコレ、何と呼ばれているか分かりますか。 “人をダメにする機械”と呼ばれているんですよ」。技術者にとって最高の褒め言葉だと思いましたね。
通販の新時代を担う画期的な段ボールケーサー
京都製作所ではこれまで、様々な段ボールケーサーを開発してきました。段ボールシートを瞬時に製函し、商品の充填・封緘までを全自動で行う装置です。製造業向けなら、例えば2リットルのペットボトルを6本ずつ箱に詰める場合、6本が入る大きさの段ボール箱を組み立て続ければOKです。しかしこの開発は「通販向け」。物流ライン上を様々な形状・大きさの商品がランダムに流れてくる中、それぞれに合わせた大きさの段ボール箱を、一台の機械で製函できるようにというオーダーでした。
流れてくる商品のLWH(長さ・幅・高さ)データから兼用データを取得し、どう制御に落としこむか。トラブル復旧時に復帰するデータをどう扱うか。複雑なロジックを機械設計と一緒に協議したため、構想だけでかなりの時間を要しました。さらに量産化を見据え、最初から立上手順・調整手順などの資料も並行して作成。文字だけでは説明が難しい部分は、イラストなどを駆使して詳細説明書を仕上げました。運用におけるイレギュラーテストでは、ソフトのデバッグ(バグや不具合の発見・修正)を時間の許す限り実施。しかしこれまで体験したことがない複雑さで、不具合が発生する条件や修復のための対策回路を四六時中考える日々が続きました。
またユーザーとなる通販業界の方が機械操作になれていないというのも、大きな課題でした。高難度の装置を、いかに誰でも操作できるようにするか。トラブル発生時に必要な自動復旧処理をプログラムしたり、操作手順をタッチパネル上でランプの点灯で分かりやすくしたり…。基本的に考える操作をさせない仕組みを目指し、検証と改善を繰り返しました。苦労の末の完成となりましたが、この開発が「使い勝手がよい機械とは何か」を、あらためて深く考えさせられる機会になりました。
設計者の「腕の見せ所」が満載の環境です
京都製作所は一人の設計者がお客様と1対1で向き合い、最後まで責任と裁量を持って開発をやり遂げる会社で、結果はすべてその設計者に帰結します。だから重圧もありますが、完成させたときの喜びも絶大です。確かに「こんなことができるのか」という難しい課題も少なくありません。でもそれは言い換えれば、すべて「設計者の腕の見せ所」。つまり設計者として技術力を試せる場面、力量を示せる瞬間、そして成長できるチャンスが豊富にあるということです。いま、「やりたい仕事ができていない」、「大きな仕事を任せてもらえない」、「なかなかスキルアップできない」という状況に置かれている設計者には、ぜひおおすめしたい仕事環境です。
京都製作所についてもっと詳しく知りたい方はこちらもご覧ください